The processes of superficial alteration depend on physical conditions, environment, geologic history and chemical and mineralogical composition. Superficial alteration is confined particularly to the zone of shallow circulation, as this is the zone of solution; its rocks are open and the circulation within it is comparatively rapid. The enrichment of ore deposits in this zone, therefore, is of special interest.
The depth of the vadose, or zone of shallow circulation, is variable, because its lower limit depends on the variable level of ground water. In moist, hilly countries its depth varies from a few feet to several hundred feet. In arid regions where the rainfall is low and evaporation great, this zone may extend to much greater depths. Permeability of the deposits is essential to the downward migration of metals. In rocks, that have been fractured since the primary ore was deposited, there is generally more extensive and deeper enrichment than in ore deposits that have been but slightly fractured. A warm climate increases chemical action and abundant rain fall is favorable to enrichment. Low relief and slow erosion give long periods of weathering and thorough leaching.
POROSITY OF ENRICHED ORES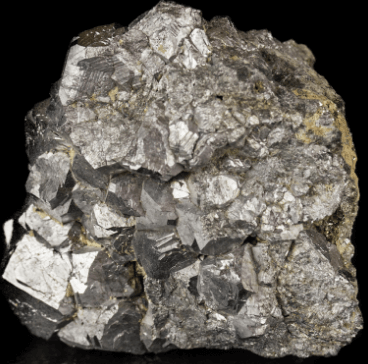
Ores enriched by precipitation or substitution of certain metals are porous and open textured, particularly in the oxidized zone. They usually show characteristic changes downward; a leached zone near the surface grading into enriched oxides just above the zone of saturation; this grading into a zone of enriched sulfides of higher grade, and this into a zone of primary ore. In moist countries, the zone of secondary or enriched sulfides usually is below the ground-water level. In arid countries, it may be partly or entirely above the ground-water level.
A porous leached outcrop stained with iron will suggest secondary ore below, and a great many deposits are found by following downward nearly barren gossans. Few, if any, silver mines have been discovered of which the outcrops have not shown silver content to some extent.
Rain water carries some carbon dioxide, which renders it a more active agent. When it enters the soil, organic compounds go into solution. The alkali metals, sodium and potassium, are readily dissolved; magnesium and the alkaline earths, barium, calcium and strontium, are attacked, and calcium and magnesium go into solution. The underground waters, then, are chiefly carbonates, chlorides and sulfates of the alkali metals, alkaline earths and other metals. Hot waters in areas of recent volcanism are chloride waters. Under the action of these waters new minerals are formed, especially oxides, hydroxides and carbonates, but most carbonates are unstable under conditions of thorough weathering. The iron carbonate is almost instantly oxidized, forming a visible rusty coating of ferric hydroxide. The lime and magnesia and alkali salts remain partly in solution, to be washed away with much of the dissolved silica.
As silver is transported mostly in the form of the silver sulfate, the source of sulfuric acid is of importance. The iron minerals are the most important sources of sulfuric acid because some of them contain more sulfur than is necessary to balance iron when iron sulfate is formed, and because iron sulfates in the presence of oxygen form ferric sulfate, a powerful and energetic solvent. Ferric sulfate hydrolizes, giving basic ferric sulfate and ultimately limonite.
Native silver, is dissolved in dilute sulfuric acid. The solubility of its sulfide, which is only slightly soluble in dilute sulfuric acid, is greatly increased in the presence of ferric sulfate, manganese dioxide or other oxidizing agents. Silver does not form stable carbonates, sulfates or oxides in the oxidizing zone; its chloride is comparatively insoluble. Silver shows little solution or transportation in deposits that carry no appreciable iron sulfides. This statement also applies to the enrichment of other minerals.
THE SILVER HALIDES
Notwithstanding the low solubilities of the silver halides and the nearly universal presence of chlorine in mineral waters, it seldom happens that all the silver dissolved in the upper parts of an argentiferous deposit is fixed as halides (bromide, chloride, iodide). The formation of the chloride near the surface does not entirely inhibit the downward migration of silver. The secondary silver sulfides are numerous and in some veins abundant. The reasons for the fairly extensive downward migration of silver even where chlorides are formed are: (1) Chlorides are present in natural waters in some deposits in amounts insufficient to precipitate as chloride all the silver that goes into solution as sulfates; (2) Silver chloride is itself slightly soluble in water; (3) Silver chloride, like other halides of silver, is soluble in an excess of alkali chlorides. Therefore, if a silver solution in the upper part of a deposit contains a small amount of alkali chloride, some silver will be fixed as chloride, but if it contains sufficient alkali chloride, horn silver will be dissolved and will migrate downward with the other metals.
The order of the solubility of the silver halides/is chloride, bromide and iodide. All of them are sparingly soluble in water, consequently the halogens precipitate silver from sulfate solutions and the halides may remain in the upper portions of the deposit and give a considerable enrichment at or near the surface.
The carbonate of silver is fairly insoluble but with excess of carbon dioxide under moderate pressure its solubility is greatly increased. This may reach a point where the carbonate is an effective carrier of silver. The great depth to which silver compounds, compared with gold, is carried downward in deposits where calcite and other carbonates abound suggests that the carbonate is an agent of transportation. The precipitation of silver is not retarded by the presence of a large excess of copper sulfate nor by the presence of zinc sulfate. The reaction with chalcocite will go on in the presence of ferric sulfate. In lead-silver ores, the galena is generally richer in silver in the oxidized zone than at greater depths. Kaolin and orthoclase will slowly precipitate silver from solution.
PRECIPITATING ACTION OF FERROUS SALTS
Ferrous sulfate will precipitate silver from solutions of sulfuric acid and ferric sulfate in which silver is present as sulfate. As ferrous sulfate increases and ferric sulfate decreases, the silver held in solution decreases; and with only ferrous sulfate in solution, all of the silver is precipitated. Ferric sulfate will inhibit the precipitation of silver from its sulfate solutions in contact with many sulfides. Hydrogen sulfide and alkaline sulfides precipitate silver from acid solutions.
Silver is carried downward by stages, doubtless, repeatedly going into solution and being precipitated until finally it reaches an environment in which it is more stable either as native silver, as argentite or as one of the complex silver salts. As depth increases the conditions become more and more favorable to its stability; by increase of ferrous and decrease of ferric sulfate, by decrease of acidity by generation of hydrogen sulfide and alkaline sulfides. Any native silver or argentite precipitated near the surface will be redissolved so long as ferric sulfate is present even in minute quantities.
Though there is no invariable rule respecting the relation of the silver chloride, the native metal, the sulfide and the arsenic and antimony sulfosalts in deposits containing all of these minerals, in many deposits these minerals have fairly well defined horizons. The chloride is most abundantly developed above the argentite ore; the antimony and arsenic sulfosalts are found at depths below the zone where argentite is most abundant, but some argentite is found with them. The native metal is found with the chloride and overlapping the zone of the chloride ores; it extends downward with argentite.
In view of the rapidity with which certain minerals decrease acidity and reduce ferric to ferrous iron, one would suppose that deposits containing such minerals in quantities would be enriched to shallower depths than deposits containing the more nearly inert minerals; that deposits containing much pyrrhotite would precipitate silver rapidly and the accumulation of ferrous sulfate in them would prevent the resolution and downward transfer of the silver.
Certain minerals may be grouped in the order of their reactivity, as follows:
Group 1.—Pyrrhotite, chalcocite, enargite, the alkali-rich silicates, leucite, nepheline and the iron silicates, olivine, augite and hornblende.
Group 2.—Galena and sphalerite and the gangue minerals fluorite, biotite and orthoclase.
Group 3.—Pyrite, chalcopyrite, quartz and muscovite.
CONDITIONS GOVERNING ENRICHMENT
Deposits composed of groups 2 and 3, other conditions being equal, should be more deeply enriched than deposits containing appreciable quantities of pyrrhotite or other minerals of group 1, and the enrichment would not be concentrated in so small a vertical range. Most silver deposits contain some sphalerite and galena and such combinations would cause precipitation at moderate rates and enrichment at intermediate depths. Silver is not precipitated from very dilute silver sulfate by calcite, siderite or rhodochrosite. If a solution of silver sulfate is acid, they will neutralize it, but carbon dioxide is released and the silver remains in solution probably as bicarbon¬ate. Even alkali carbonates do not remove all of the silver from solution. Metallic sulfides in the presence of carbonates will precipitate the silver, the most efficient being pyrrhotite, chalcocite and others acting more rapidly than the inert sulfides, such as pyrite.
OUTCROPS
Outcrops of silver deposits may carry silver in concentrated form or may be partly leached of the metal. If the leaching waters carry much chloride, silver will be greatly concentrated at the outcrops, particularly in arid or semi-arid countries. In arid countries smaller amounts of water will percolate through the ore than in wet regions. Many silver deposits are enormously rich at their outcrop but profitless below a depth of 100 ft. Silver chloride forms in moderate, amounts in comparatively moist countries.
The concentration of silver as chloride or native metal at the outcrop and in the superficial zone at many places is attended by concentration of the gold, probably because of a decrease in the volume of the ore and gangue minerals by weathering. If the deposit contains manganese, gold may be carried downward and be redeposited below. In general, however, gold is more readily precipitated than silver, except the chloride of silver, especially where the silver-gold ore has a calcite gangue.
SILVER-LEAD DEPOSITS
A common type of silver ore is composed of argentiferous galena, pyrite, sphalerite and other minerals. The zinc is leached out by weathering, leaving the lead and silver in a concentrated form. If the deposits are in the limestone, the zinc is precipitated extensively as carbonate along fractures and bedding planes, extending outward and downward from the altered silver-lead ore.
SILVER-COPPER DEPOSITS
Silver and gold may be found in notable concentration at the outcrops of copper deposits that carry little or no copper at the surface, as at Butte, Mont. In general, secondary silver minerals and gold are precipitated nearer the surface than secondary copper minerals. Copper may be held in solution as sulfate in the presence of ferrous sulfate, but the ferrous salt precipitates silver and gold, so that silver and gold will be thrown out of a solution that is depositing chalcocite. Moreover, chalcocite itself precipitates gold and silver almost instantly. It follows that in copper deposits no precious metals of secondary origin will be found below an extensive chalcocite zone. At Butte, the superficial secondary silver ores graded downward into secondary copper ores.
Mining and Metallurgy in Foreign Countries
European smelting charges for galena concentrates at present range from 50 to 60 shillings per metric
ton, according to the quality of the ore. In European lead-smelting practice, full payment is made for the
lead and silver contents of the ore, losses thereof being absorbed in the treatment charge. American silver-lead smelters distribute their costs and losses through a complicated schedule. The American sellers of lead ores would experience a feeling of faintness at the sight of the foreign treatment charges. Their psychology has stood in the way of simplified terms for lead smelting in the United States.
Recently the Spanish Government imposed an export duty amounting to 20 (gold) pesetas per metric ton on copper in matte and 50 pesetas on copper in ingots and cathodes. This led the Rio Tinto Copper Co., which previously had been producing blister copper, to cease operating its converters and begin the exportation of all of its copper in the form of matte, which now goes to Welsh smelters.
At the last annual meeting of the share-holders of the Zinc Corporation Limited, F. A. Govett, the managing director, did not mince matters as regards the effect of trade-union restrictions, the domination of which he rightly characterized as “nothing more nor less than cast-iron tyranny.” It is to this tyranny, of course, that the world shortage in the supplies of lead is entirely due. As to the prospects for lead, Mr. Govett remarked that the stocks are low, but consumption is not large. Nevertheless, taking Europe and America together, it is expanding, though with the world in ruins it cannot be great enough to absorb any very large production. The mines being shut down, the remaining stocks are being consumed, and as they disappear, those who can produce cheaply will be able to profit by this fact, but a 35-hr. week and the present rates of pay render cheap output impossible in Australia. To be reasonably safe, he remarked, Broken Hill must be able to produce lead at under £20 a ton, in order to compete.
The Hon. W. L. Baillieu, chairman of the Broken Hill Associated Smelters and of the Electrolytic Zinc Co. of Australasia, in a recent interview with the Mining Journal of London, expressed himself rather more optimistically, as follows:
Broken Hill has been disturbed since the middle of 1919 by serious labor troubles. A.special tribunal was created to deal with the dispute, and its award was made under the combined influences of the excessively high metal prices of 1920 and allegations against the conditions under which mining was carried on. A technical committee was. appointed by the N.S.W. Government to deal with these allegations; it has just issued its report, which in the main is satisfactory to the companies. In the meantime, the companies have been working under the oppressive award of 1920. It was agreed, however, when this award was made, that it should be revised when the technical committee had made its report. This having been done, I expect a revision to be made just as soon as it is possible to get the machinery of the court into operation.
The costs of smelting in Australia, by reason of the very high metallurgical efficiency of the Port Pirie plant, compare favorably with those of other countries. Coal and transport costs have been maintained at an unduly high level, but these are tending lower; every month sees a decline, and this must continue. The only shareholders in the Broken Hill Associated Smelters are the Broken Hill Proprietary, North Broken Hill, Zinc Corporation, South Broken Hill, and British Broken Hill. There are no private shareholders, and all the companies sell their output under identical contracts to the smelter.
There are roughly 15,000,000 tons of ore blocked out in Broken Hill, and every indication of about a similar quantity to follow before this great field is worked out. It is true that after 40 years of production it is past its prime, taken collectively, but mines like the South, North, British, and Zinc Corporation are capable of developing to even more important concerns than they are to-day.
In 1905 we started zinc concentration at Broken Hill with 13,000,000 tons of zinciferous residues in stacks, plus the current output. By the middle of 1923 the dumps or stacks will be “cut out.” This means that after that date we will have to rely on the output of “current ore” only for the zinc-concentrating plants. We have in the pre-war days turned out as much as 500,000 tons of zinc concentrates per annum; in the future we should run about 300,000 tons per annum, subject to lead prices enabling the crude ore to be first profitably treated for lead.
The Electrolytic Zinc Co., which is now producing refined zinc at the rate of 25,000 tons a year, will, when the second half of the power contracted for is supplied (which is expected at the end of the year), produce about 45,000 tons of high-grade spelter a year, and later will increase this total. It will also produce about 6000 tons of lead, 1,200,000 oz. of silver, 10,000 oz. of gold, 200 tons of cadmium, as well as large quantities of leaded zinc oxide, pure zinc oxide, and lithopone, as the subsidiary departments are developed. In addition, with 150,000 tons of chamber sulfuric acid a year at its command, its interests and influence in the super-phosphate and chemical industries must become very great.
There are considerable possibilities in New Guinea, which is controlled by Australia. Within a year she will be an important copper producer, and I look for a considerable extension of this industry, the very substantial possibilities of which are now being more widely recognized. The expert reports make it clear that New Guinea will produce copper at costs comparable with the lowest obtainable in any other country.
French engineers are reported to be engaged with the erection at Quang-Yen, in Indo-China, of a plant designed to yield 10,000 tons of spelter per annum out of an oxidized zinc ore.
It has been announced that the Italian Government has decided to raise the subsidy granted to the Sicilian sulfur industry from 100,000,000 to 120,000,000 lire, in order to assist it to meet American competition. The production of Sicilian sulfur is at present less than two- thirds of the pre-war figure.
Disposal of Blast-furnace Slag
Numerous devices and processes have been devised to dispose of blast-furnace slag. However, most methods are expensive and fail to produce the desired results. The idea presented here has been under consideration for some time, and is protected by recent patents.
For utilization of blast-furnace slag, the following scheme is proposed.
- Discharge slag directly from furnace into cars, which contain several feet of water.
- Place disintegrated slag in centrifugal drier.
- Run product through pulverizer, crushing slag so that 75 per cent, will pass through a 100-mesh sieve.
- Mix one part of cement with 12 parts of powdered slag, adding small amount of water.
- Mold the resulting mixture in bricks of standard size, in presses.
Bricks produced from blast-furnace slag have been tested at the Fritz Engineering Laboratory at Lehigh University by E. P. Gangewere, with the following results:
Transverse Test.—Supports 5/8 in. from each end. Width 2 5/16 in., depth 4 in. Span 7 in. Average breaking load, 7000 lb.
Compression Test.—Bricks were set on edge, after being broken in half. The following area was subjected to compression: Length 4 3/16 in., breadth 2 5/16 in. Average breaking load, 80,000 lb., or ultimate strength of 8500 lb. per sq. in.
Absorption Test.—In a period of 11 days, the bricks absorbed 7.15 per cent, of their weight in moisture.
Shearing Test.—When subjected to a double shearing test, they failed at unit load of 1650 lb. per sq. in.
These tests show that bricks produced from blast-furnace slag have a strength far above the average produced from shale or clay. The texture of the bricks is uniform, and an even, smooth surface results from this method of manufacture.
The cost of producing this product is far less than that of making bricks from clay or shale, as the whole process can be operated in conjunction with the blast furnaces of any steel plant.
Numbering Iron or Aluminum Castings
The National Automobile Underwriters Conference submitted to the National Automobile Chamber of
Commerce an offer of a 20 per cent, reduction in automobile insurance theft rates, if satisfactory methods of numbering engines and frames should be perfected. This offer was submitted by Charles Clifton, president of the National Automobile Chamber of Commerce, to the Society of Automotive Engineers.
The work on developing a satisfactory method of numbering engines and frames was assigned by the
Council of the Society to two committees, one made up of engineering representatives of passenger-car manufacturers and the other of the engineering representatives of engine manufacturers. More than twenty suggestions have been received to date and are being tested to determine their relative merits. Further suggestions are desired and should be sent to the Society of Automotive Engineers, 29 West 39th St., New York City.
Some of the methods proposed which are now being tested are: Casting numbers on the crankcase; concentric expanded disks; a special alloy cast in the crankcase; a checker-board system; a small thin fin cast on the crankcase on which numbers could be stamped (the numbered fin would be broken off by the dealer and held for the purchaser); raised number-plates welded to the frame; armor-plate number-plates riveted on, using two or more rivets which enter into the frame construction; fairly large numbers embossed deeply into the frame; small holes punched or drilled into the frames at places where the frames would not be weakened; a thumb-print system; an armored plate riveted into position, with special seals placed over the rivets, case-hardened plugs or plates bearing the numbers, fastened into the frame or engine with blind screws or some other such devices; a series of embossed nickel plates set
somewhere in the frame or in the engine in such a way that they could not be removed without tearing down the engine or frame, nickel, being advocated as it is not easily affected by the acetylene torch.